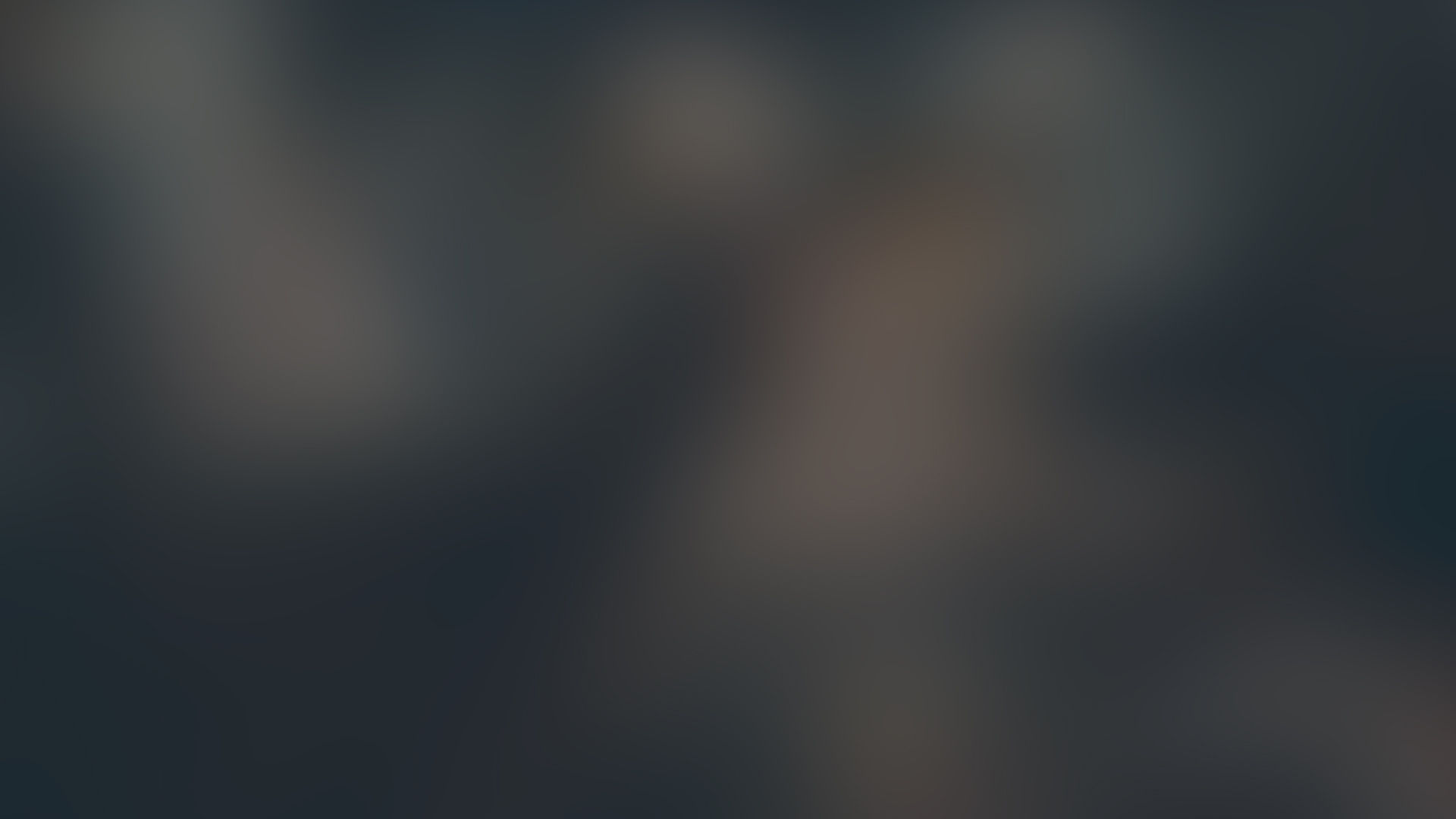


TOOL & DIE
ENGINEERING
Tool & Die Dynamics
Precision in Production
Tool and die engineering is the backbone of manufacturing, crafting precision tools that shape raw materials into finished products. From intricate molds to custom dies, these engineered solutions ensure efficiency and accuracy, driving innovation and reliability across industries like automotive, aerospace, and electronics.
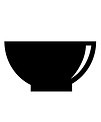
Complex Shapes

Cost-Effective

High Production Rates

Strength and Durability
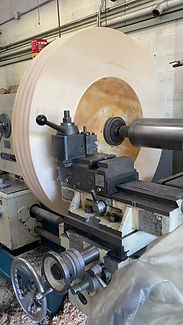
HOW IT WORKS
Tool and die engineering involves designing and manufacturing specialized tools, molds, and dies used in various manufacturing processes. Engineers create precise specifications for these tools, which are then machined or fabricated to produce components with accuracy and efficiency. Tool and die engineering plays a crucial role in industries such as automotive, aerospace, and electronics by ensuring the quality and consistency of manufactured parts.
APPLICATIONS​
​
-
METAL STAMPING: Tool and die sets are extensively used in metal stamping processes to produce components with complex shapes and tight tolerances. Industries such as automotive, aerospace, electronics, and appliance manufacturing rely on metal stamping for producing parts like panels, brackets, connectors, and housings.
-
INJECTION MOLDING: Injection molding is a widely used manufacturing process for producing plastic parts in large volumes. Tool and die sets, known as molds, are used to shape molten plastic material into desired forms. Injection molded parts are found in diverse products ranging from automotive components and consumer electronics to medical devices and packaging.
-
DIE CASTING: Die casting is a manufacturing process for producing metal parts by forcing molten metal under high pressure into reusable steel molds, called dies. Tool and die sets are crucial for designing and producing these dies, which are used in industries such as automotive, aerospace, and consumer goods for producing components like engine parts, housings, and structural components.
-
EXTRUSION: Extrusion processes involve forcing material through a die to create continuous shapes with a uniform cross-section. Tool and die engineering is essential for designing and manufacturing extrusion dies used in processes such as plastic extrusion, aluminum extrusion, and profile extrusion for producing items like pipes, tubes, profiles, and rods.
-
FORMING AND FORGING: Tool and die sets are used in forming and forging processes to shape metal blanks into desired shapes through compression or deformation. Applications include producing automotive components, aerospace parts, hand tools, and industrial machinery components.
-
SHEET METAL FABRICATION: Tool and die engineering plays a vital role in sheet metal fabrication processes such as bending, punching, shearing, and blanking. Tool and die sets are used to create dies, punches, and forming tools for producing a wide range of sheet metal components used in construction, appliances, furniture, and electronics.
-
PROTOTYPING AND RAPID TOOLING: Tool and die engineering is also used in prototyping and rapid tooling processes to create prototype parts and molds for testing and validation purposes before full-scale production. Rapid prototyping techniques such as additive manufacturing (3D printing) can be combined with traditional tool and die methods to accelerate product development cycles.
MATERIALS
​
-
TOOL STEEL: Tool steels are specially designed high-carbon steels with additional alloying elements such as chromium, vanadium, tungsten, or molybdenum to enhance hardness, wear resistance, and toughness. They are commonly used for making cutting tools, dies, and molds in various manufacturing processes.
-
​
-
HIGH SPEED STEEL (HSS): High-speed steels are alloy steels designed to withstand high temperatures and maintain cutting edge hardness at elevated speeds. They are often used for cutting tools, drills, and milling cutters in machining operations.
-
​
-
CARBIDE: Carbide materials, such as tungsten carbide (WC), are extremely hard and wear-resistant, making them suitable for cutting tools, inserts, and wear parts in high-speed machining and metal forming applications.
-
​
-
CERAMIC: Ceramics offer high hardness, wear resistance, and thermal stability, making them suitable for specialized cutting tools and wear parts in high-temperature and abrasive machining applications.
-
​
-
CEMENTED CARBIDES (Hardmetal): Cemented carbides are composite materials composed of hard carbide particles (e.g., tungsten carbide) bonded together with a tough metallic binder (e.g., cobalt). They are commonly used for cutting tools, dies, and wear parts in metalworking and mining industries.
-
​
-
DIE STEEL: Die steels are high-strength steels specifically designed for making dies and molds used in metal forming, casting, and extrusion processes. They often contain alloying elements such as chromium, molybdenum, and vanadium to enhance hardness, wear resistance, and toughness.
-
​
-
ALUMINUM BRONZE: Aluminum bronze alloys offer good wear resistance, corrosion resistance, and thermal conductivity, making them suitable for making die casting molds and components subjected to high pressures and temperatures.
-
​
-
CAST IRON: Cast iron materials, such as gray cast iron and ductile iron, are used for making large and complex dies, molds, and machine components due to their good machinability, wear resistance, and damping properties.